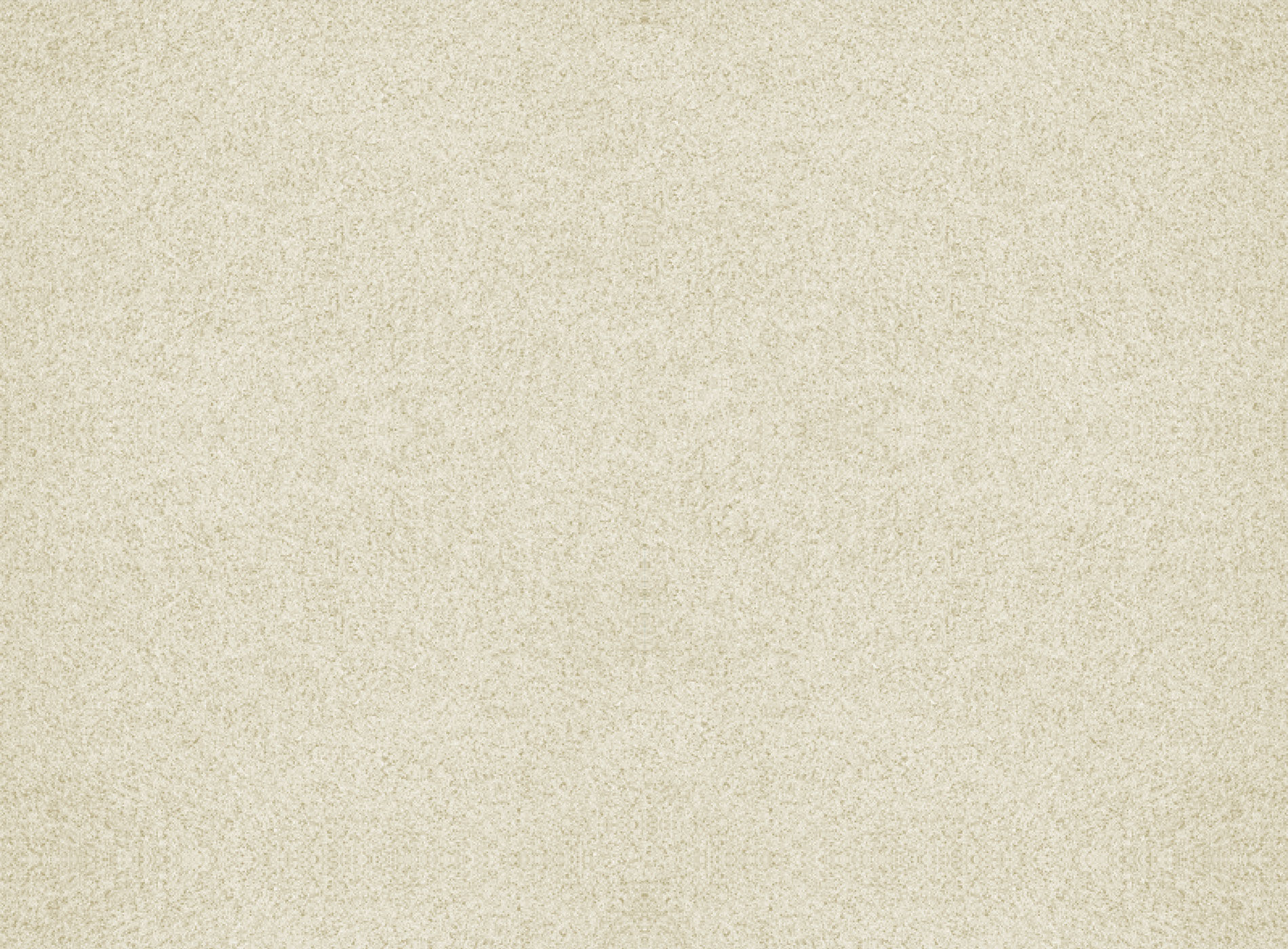
Inicio >> BPM (Buenas Practicas de Manufactura)
BPM (BUENAS PRACTICAS DE MANUFACTURA)

Son los principios básicos y prácticas generales de higiene en la manipulación, preparación, elaboración, envasado, almacenamiento, transporte y distribución de alimentos para consumo humano, con el objeto de garantizar que los productos se fabriquen en condiciones sanitarias adecuadas y se disminuyan los riesgos inherentes a la producción.
El manual de Manual de BPM debe contener los siguientes temas:
1. Disposiciones generales
2. Edificación e instalaciones
3. Equipos y utensilios
4. Personal manipulador
5. Requisitos higiénicos de fabricación
6. Aseguramiento y Control de Calidad
7. Saneamiento
8. Distribución de alimentos
2. BPM - En instalaciones
Las BPM en las instalaciones deben estar enfoncadas en los siguientes aspectos:
-
Localización y accesos
-
Diseño y construcción
-
Disposición de residuos
-
Instalaciones sanitarias
-
Pisos, paredes, y techos
-
Ventanas y puertas
-
Iluminación y ventilación
3. BPM - Equipos y Utensilios
-
Diseño acorde a su función
-
Fabricados en materiales resistentes a la corrosión
-
No tener materiales porosos o con grietas
-
De fácil lavado y desinfección
-
Equipos que sean de fácil inspección

4. Manipulador de Alimentos
Definición: Toda persona que interviene directamente y aunque sea en forma ocasional, en actividades de fabricación, procesamiento, preparación, envase, almacenamiento, transporte y expendio de alimentos.
Estado de Salud:
-
Reconocimiento médico inicial
-
Ausencia de enfermedades que se transmitan por los alimentos
-
Informar si se tienen heridas abiertas, irritaciones cutáneas infectadas o diarrea.
Educación y capacitación:
-
Tener información en prácticas higiénicas en la manipulación de alimentos.
-
Capacitación continua y permanente
-
Colocar avisos para enfatizar lavado de manos
Practica higiénicas:
-
Limpieza e higiene personal
-
Lavado de manos con desinfectante
-
Mantener cabello recogido
-
Mantener uñas cortas, limpias y sin esmalte
-
Usar calzado cerrado
-
Uso de guantes cuando sea necesario
-
Uso obligatorio de tapabocas
-
No uso de joyería, relojes y otros accesorios
-
No comer ni beber en las zonas de producción

4. Requisitos Higiénicos de Fabricación
Óptimas condiciones sanitarias
-
Control de condiciones - t, T°
-
Procedimientos de control para procesos (refrigeración, cocción)
-
Proteger alimentos para evitar la contamincación
Prevención de contaminación cruzada
-
Cumplimiento de las normas higiénico-sanitarias para todo el personal manipulador de alimentos
-
Evitar contacto directo de Materias Primas con el producto termina
do, ya sea a partir del uso de utensilios sucios o por contacto del producto terminado con materias primas.
5. Aseguramiento y Control de Calidad
HACCP (Analisis de Peligro y puntos de control)
Punto critico de control (CCP)
Un Punto Crítico de Control es un punto, dentro del proceso de manipulación, en el que el Riesgo debe ser controlado, eliminado o reducido a un nivel seguro.
Proceso operacional Estandar
-
Es el procedimiento preventivo de control quedebe estar directa o indirectamente relacionado con Seguridad Alimentaria.
-
Las SOPs deben ser controladas confrecuencias fijas y en momentos predeterminados
-
Los cotroles SOP no son definidos por muestreo o por lotes

Analisis de Riesgos
Es un mètodo para identificar riesgos a la seguridad alimentaria en cada fase de manipulaciòn.
¿Què son los limites criticos?
Los limites crìticos son limites especificos de las propiedades de los alimentos, tal como:
-
Tiempo y temperatura
-
PH
-
Olor, Sabor, Color.
En un catering, los lìmites de control son màs frecuentemente la relaciòn tiempo/ temperatura sobre los diferentes pasos del proceso de manipulaciòn.
Puntos criticos de Control
Temperatura de alimentos en al recepciòn
Temperaturas de almacenamiento
Temperatura de los alimentos listos para consumo durante el descongelamiento fuera de camara.
Cocciòn
Enfriamiento Ràpido
Temperatura de manipulaciòn de alimentos listos para consumo
Temperatura durante el despacho
